摘要 優化的刀具設計方案具有關鍵性的作用碳纖維增強復合材料(CFRP)具有極高的強度重量比,并且在極端條件下具有穩定的材料屬性,因此在全球航天航空行業內有著廣泛的應用。這種材料可以單獨使...
優化的刀具設計方案具有關鍵性的作用碳纖維增強復合材料(CFRP)具有極高的強度重量比,并且在極端條件下具有穩定的材料屬性,因此在全球航天航空行業內有著廣泛的應用。這種材料可以單獨使用,也可以與鈦板和鋁板配合使用。舉例而言,波音 787 夢幻客機 80% 的制造材料為復合材料,相當于其重量的 50%,可以減少1,500 張鋁板和 50,000 個固定件的使用。與波音 767 相比,可以節省 20% 的燃油消耗。目前,類如膠粘和焊接之類的聯接技術還有很多問題;因此,鉚接固定技術在實際應用中依然占有主流地位。因為碳纖維材料和金屬材料的機械性能有極大的差別,在對緊固孔進行有效的鉆孔加工時,需要使用具有高耐磨性和優化槽型的切削刀具產品。
在加工航天航空行業內的零配件時,多晶金剛石(PCD)刀具要比傳統的碳化鎢硬質合金刀具有更高的加工效率。一些領先的刀具制造商正在開發并生產 PCD 釬焊鉆頭產品。這些刀具產品的切削刃采用 PCD 材料,鉆體部分為整體硬質合金材料。硬質合金鉆體有很好的剛性和尺寸精度,確保鉆孔的加工質量,同時具有內部螺旋冷卻通道,螺旋式排屑槽可以提高冷卻性能和排屑性能,這些特性對鉆孔加工是非常必要的。位于功能區的切削刃部分采用 PCD 材料,具有極好的耐磨性,提高加工效率。
優化的刀具設計具有關鍵性的作用,在加工先進的航天航空復合材料時可以確保極好的鉆孔質量。在刀具尺寸設計中,很多必要因素對鉆孔質量都起著重大的影響作用,例如,為了降低切削力而提高刀尖半徑的銳度,增大前角等。其它因素還包括,為了減小推進力,以及避免纖維材料的撕裂現象而減小鉆尖角度,為了改善毛口高度控制性能而優化刃口設計。機床刀具、主軸及整體刀具的剛性、刀柄、內冷或射流冷卻方式,以及鉆孔工件材料在刀具設計過程中也都是需要考慮的重要因素。在多數情況下,為了滿足客戶的不同需求,需要為客戶及時提供定制刀具產品。
刀具開發過程
為了開發一款高性能的 PCD 刀具產品,應當在考慮綜合因素的情況下進行深入的研究。這種開發過程不僅決定了刀具的性能,還對刀具的加工效率和成本起到了重要的影響作用。
在生產用于復合材料加工的合成金剛石鉆頭產品時,有 4 種主要技術可以應用:
- CVD(化學氣相淀積)金剛石涂層鉆頭
整體硬質合金鉆在最后一個工藝經過 CVD 金剛石涂層處理。這是一種成本效益很好的產品,但刃口銳度受到了涂層厚度的影響。此外,因為硬質合金基體部分和金剛石涂層部分的硬度不同,這款產品吸收沖擊能量的性能不佳。防崩刃性能也很有限。
- PCD 鑲刃鉆頭
圓錐型的 PCD 材料按照特點鉆尖槽型燒結至較小尺寸的硬質合金基體之上。然后,將這些半成品釬焊至整體硬質合金鉆體之上。為了處理硬質合金和 PCD 聯接面之間的高應力問題,這款 PCD 產品在 PCD 材質優化方面受到了限制。后燒結工藝還會導致成本高昂,因為需要去除非功能區的金剛石材料,還要增加內部冷卻孔。
- PCD 紋絡鉆頭
在整體硬質合金棒料之上預先加工的槽內填入 PCD 粉末原料,然后經過高溫高壓處理形成 PCD 排列結構。在經過高溫高壓過
程之后,對棒料進行剪切后釬焊至鉆體之上,最后按照規定槽型進行磨削處理。這種 PCD 紋絡技術可以制造復雜槽型,以及具有高正前角外形的刀具產品;與 PCD 鑲刃刀具產品相比,只需較少的磨削處理。這種刀具受到尺寸限制,因為要對復雜 3D 槽型進行高溫高壓處理。此外,因通常需要使用高鈷成分的材料,因此也降低了 PCD 材料的硬度和耐磨性。
- PCD 釬焊鉆頭
最成熟的 PCD 鉆頭加工技術為 2D 技術(例如 PCD 扁鉆) 對于較小尺寸刀具,可以使用一種特殊的硬質合金和 PCD 夾層材料;對于較大尺寸刀具,可以使用純 PCD 鉆尖材料。這款產品在槽型方面有嚴重的缺陷,因為很難增加一個用于復合材料加工的前角。3D 釬焊需要多個所需材質的 PCD 刀座,并且微觀結構應按照設計切割為螺旋形狀。在整體硬質合金鉆頭上應磨削出一個對應的螺旋槽,以安裝 PCD 刀片。與 PCD 鑲刃產品相比,這款 3D 釬焊產品只在功能區采用 PCD 材料,大大增加了加工性能。這項 3D 釬焊技術被用于開發本文所述的 PCD 測試鉆頭。
選擇 PCD 材質的另一個重要因素是金剛石材料的機械加工性能。機械加工性能是通過計算由不同 PCD 原材料制成相同刀具的時間評定的。重點關注各個制造步驟,包括 PCD 刀盤的腐蝕和 PCD 材料的磨削。了解機械加工性能測試結果請參看表一中的測定等級。機械加工性能越好,等級就越高,制造時間就越短,成本也就越低;這與在開發一款具有競爭性的刀具產品時,刀具性能的重要性是一樣的。
PCD 釬焊
本文中介紹的刀具產品需要將 PCD 螺旋切片釬焊至碳化鎢刀體上,選用的釬焊技術應避免處于亞穩態的多晶金剛石石墨化,還需要將 PCD 與碳化鎢進行粘結處理。這需要采用高效的釬焊技術。高效的釬焊材料通常包括高熔點聚合物材料,如鈦材料。釬焊溫度因此很高,對金剛石相的穩定性有負面影響。為了避免石墨化,在釬焊過程中應避免氧化環境。最新的技術包括氬氣環境中的感應釬焊,以及真空釬焊。
優化的刀具槽型
在對復合材料/鈦材料層疊板進行鉆孔加工時,選擇優化的刀具槽型非常困難,因為這兩種材料在切削過程中表現出不同的特性。CFRP 材料的鉆孔加工通常需要大螺旋角和長切削刃,因為碳纖維應當沿著切削刃發生剪切作用。長切削刃通過小鉆尖角而實現。此外,CFRP 材料的鉆孔加工還應降低軸向力,以避免在退刀時發生加工材料層裂現象。這些特點可以形成非常鋒利的切削刃槽型,同時也減小楔塊角度。后角可以高達 20 度,螺旋角約為 30 度。鈦材料的切削原則上也可使用鋒利的切削刃,但與 CFRP 材料的鉆孔加工相比,需要一個更加穩定的楔塊角。鈦材料加工中的刀具后角通常在 8-14 度之間的范圍。與鋼材料加工相比,這些后角通常更大(在本文展示產品中約為 12 度),因為后刀面上的熱量應當盡可能降低,一減少刀側面磨耗的形成。大后角與典型的 30 度螺旋角結合應用時,會明顯降低切削刃的強度。螺旋角已減小至 15-20 度范圍,從而可對大后角做出平衡。本文展示的這項制造工藝可以根據所需刀具槽型,選擇不同的螺旋角。這是本文展示工藝的主要優勢之一,因為普通的 PCD 刀尖鑲刃刀具允許使用的最大螺旋角僅為 8 度。
為了實現孔徑緊密公差,鉆尖應當具備卓越的自定中心性能,這一點是絕對必要的。從另一個角度而言,鉆尖角度對毛刺的形成也起到重要的影響。我們知道,鉆尖角在低于 90 度或高于 150 度時,可以幫助降低鉆孔出口處的毛刺高度。因此,鉆尖角為 155 度的鉆頭適合鈦材料加工的需求,但定中心性能不好。所以,推薦使用雙鉆尖角設計方案,其中內部鉆尖角為 130 度,外部鉆尖角為 155 度。與普通應用的長切削刃鉆頭相比,這款鉆頭產品的整體鉆尖高度較低。因此,第三條和第四條刃帶可以很快接觸材料,有益于形成更緊密的孔徑公差。
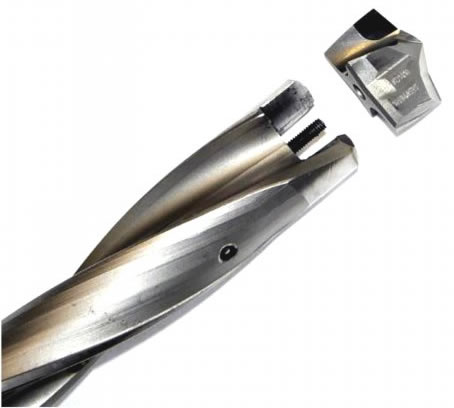
采用 PCD 釬焊刀片的定制模塊化鉆頭
實驗性研究
這款開發的 PCD 刀具產品經過了實驗性測試,目的在于評估在規定應用中最合適的 PCD 材質和刀具槽型。測試過程中的刀具設置和切削參數如下。
- 測試刀具
PCD 釬焊鉆頭,直徑為 11.113 毫米(7/16 英寸),三種不同的 PCD 材質(G4、KD1415,和 KD1425),未經涂層處理相同槽型的鉆頭。
- 測試材料
測試材料包括一塊厚度為 8.7 毫米(0.342 英寸)的購置 CFRP 板材(Isocarbon 3k),并與一塊 厚度為 10.8 毫米(0.425 英寸)的 Ti-6Al-4V 板材牢固地層疊在一起。使用測試刀具進行通孔加工,從 CFRP 側進刀,從鈦板側出刀
- 機床刀具及冷卻劑
一臺 CNC 加工中心(Heckert CWK 400),水平主軸,主軸貫通式微量潤滑方式(Vascomill MMS FA2)。
- 切削參數
切削速度為 20 米/分鐘(65 SFM),進給率為 0.05 毫米/轉(0.002 ipr),同時適用于 CFRP 和鈦材料加工。不使用啄鉆加工法。
- 刀具檢測
為了監控刀具磨損過程,在完成 4 個孔的鉆孔加工后,使用顯微鏡對鉆頭進行檢測。在完成 24 個孔的鉆孔加工后,在掃描電子顯微鏡下觀察刀具的磨耗結構。
- 鉆孔測量
在完成所有加工測試后,對測試材料進行清洗和標注。對所有鉆孔進行檢測。對 4 個孔的內部進行直徑測量(兩個在 CFRP 板材的進口處和出口處附近,兩個在 鈦板材的相同位置)。同時還對鈦板材底部出口孔表面的毛刺高度進行測量。
結果及分析
超長、可預測,以及穩定的使用壽命是決定刀具產品是否能夠贏得客戶的主要因素。在對 CFRP/Ti 復合基體材料進行鉆孔加工時,為了獲得滿意的鉆孔質量,必須同時滿足幾個要求。鉆孔尺徑為緊公差尺寸,以安裝緊固件,鉆孔出口處的毛刺高度必須符合規定要求,以減輕或避免去毛刺工序。為了避免因刀具突變失效而導致的鉆孔損壞,并盡力維護刀具的可修磨性,鉆尖的崩刃現象必須盡可能降低,并對其進行監控。以下標準被用來作為確定測試刀具是否已達到使用壽命極限:
a)鉆孔尺寸公差為 11.113 + 70 微米(H10);
b)毛刺尺寸為 0.2 毫米;
c)出現鉆尖崩刃
測試表明,PCD 鉆頭在使用壽命即將結束時的主要失效模式是鉆尖出現崩刃;。
硬質合金鉆的失效模式表現為毛刺高度超限。在這次測試中,所有鉆孔都符合鉆孔質量要求。
鉆孔尺寸
圖一顯示內容為測試 PCD 刀具的鉆孔加工尺寸。在對每個鉆孔檢測時,孔徑的測量位置選擇在 4 個不同的位置;2 個在 CFRP 板材部位,2 個在鈦板材部位;分別對應在鉆孔進口表面和出口表面。
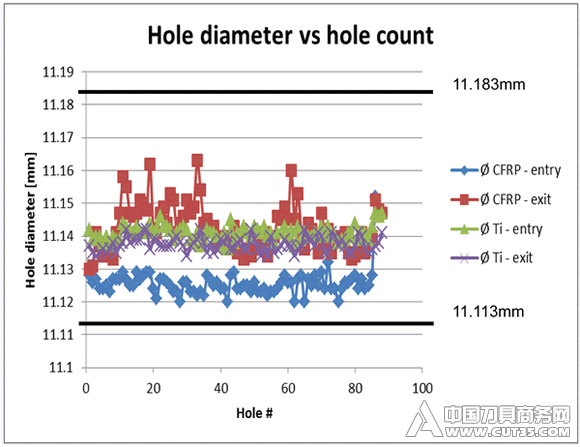
圖一:一款 PCD 刀具加工鉆孔數與尺徑的對比
可以看出,位于鈦板材部位的鉆孔質量非常好,尺寸在規定公差值的中間范圍,上下浮動范圍很小,為10 微米。鈦板材鉆孔入口處和出口處的尺寸非常接近。但在 CFRP 板材部位,鉆孔入口處和出口處的孔徑差較大。這種現象是因為在排屑過程中,切屑對鉆孔避刮擦造成的結果。對于減少切屑的刮擦,以及增加鉆孔尺寸的一致性而言,提高切屑控制性能是非常必要的。僅僅依靠刀具設計而提高切屑控制性能是非常困難的。在加工實踐中,一種成熟的工藝是增加啄鉆操作,或是通過振動支持鉆孔操作,以實現控制切屑長度并減弱切屑刮擦效果。
測試結果表明,在此展示的新型鉆尖產品可以加工出 H10 公差等級的鉆孔尺寸。在優化加工條件以及加工過程穩定的情況下,甚至可以實現 H8 公差等級的鉆孔尺寸。不能證明鉆孔質量與切削刃材料有必然關系。相同鉆尖槽型的 PCD 鉆頭和硬質合金鉆頭的鉆孔加工質量是相似的。
毛刺
在探討與毛刺高度控制和磨損結構相關的鉆孔結果時,可以清晰地看到不同切削刃材料產生的不同結果。圖二顯示內容為一款硬質合金刀具和兩款 PCD(KD1415 和 G4 材質)刀具鉆孔加工時毛刺高度的發展過程與鉆孔數的對比情況。

圖二:因刀具磨耗導致的毛刺高度發展過程與鉆孔數的對比情況
可以看出,硬質合金鉆僅完成 14 個鉆孔加工之后,在鈦板材出口處的毛刺高度就明顯增加;而兩款 PCD 刀具在加工過程中,首次出現毛刺超過規定的鉆孔分別是第 57 個鉆孔和第 117 個鉆孔。
從理論上講,毛刺高度的發展過程與刀具鉆尖部位的磨耗緊密相關。這一點可以在硬質合金刀具和 PCD 刀具的對比中顯明,因為這兩種材料的硬度有很大的不同;所以,PCD 刀具鉆尖處的磨耗發展過程較慢。與硬質合金鉆相比,PCD 鉆的鉆尖磨耗要少得多。這三種 PCD 材質的磨耗發展情況區別很小。PCD 材質的主要磨耗類型為切削刃/鉆尖部位的崩刃。
表格一對這三種 PCD 測試材質的刀具壽命做了綜合對比。可以看出,G4 和 KD1415 材質在刀具平均壽命方面非常相似。KD1415 在刀具使用壽命的穩定性方面表現更好,并且因為機械加工性能更好,可以減少制造成本。因此在本文所述的加工應用中,被選為最適宜的材質。

結論
我們開發了三款采用不同 PCD 材質以及優化槽型的 PCD 整體硬質合金釬焊鉆頭產品,并對這些產品進行了測試。測試結論如下:
1)在 PCD 刀具制造過程中,3D 釬焊技術允許刀具采用靈活的螺旋角角度,因此也可以采用大前角設計方案。與 PCD 鑲刃產品相比,3D 釬焊產品因為去除了刀具功能區表面的 PCD 材料,所以具有更好的機械加工性能;
2)這款開發的 PCD 鉆產品采用優化的刀具槽型(雙鉆尖角度、螺旋槽、內部螺旋冷卻通道、大前角),因此可以加工高質量的鉆孔(鉆孔尺徑及毛刺高度控制)。
3)與未經涂層處理的整體硬質合金鉆相比,PCD 鉆在使用壽命方面有顯著的改善。
4)所有測試 PCD 刀具有相同的磨損形態,從前刀面出現細微裂縫開始,最終會因鉆尖崩刃導致突變性失效。
5)在刀具壽命穩定性和機械加工性能方面,KD1415 要比 G4 和 KD1425 材質有更佳的表現。所以,KD1415 是最適合本文所述加工應用的材質。
作為行業的領導者,肯納金屬公司在慶祝公司成立75周年之際,特別為在苛刻加工條件下,尋求最佳產品性能的客戶提供創新的產品解決方案,幫助客戶提高生產率。肯納金屬公司應用最先進的物料技術,為分布在60個國家,涉及航空航天、筑路與采礦、能源,以及工業生產等領域的客戶提供創新的耐磨損產品、產品和應用設計,以及應用技術服務。公司員工總數約為14,000人,銷售總額接近30億美元;公司營業收入的一半來自北美地區以外的市場;過去5年內推出新產品的銷售總額占全球銷售總額的40%。肯納金屬公司注重安全理念,曾獲得“全球最具商業道德企業” 稱號(道德村協會),“杰出創新企業”稱號 (產品研發管理協會),以及“美國最安全企業”稱號(EHS Today雜志);肯納金屬公司及其基金會持續在技術教育、工業技術,以及物料科學等領域進行投資,展現了行業發展以及經濟繁榮的魅力前景。